Proof Points of Execution
Our Markets
New Brand Experience Center in Korea
On June 9, Bystronic Korea officially inaugurated the new Brand Experience Center with a total footprint of over 3,000 square meters. The new center enables us to offer our customers throughout the entire APAC region an even better level of service.
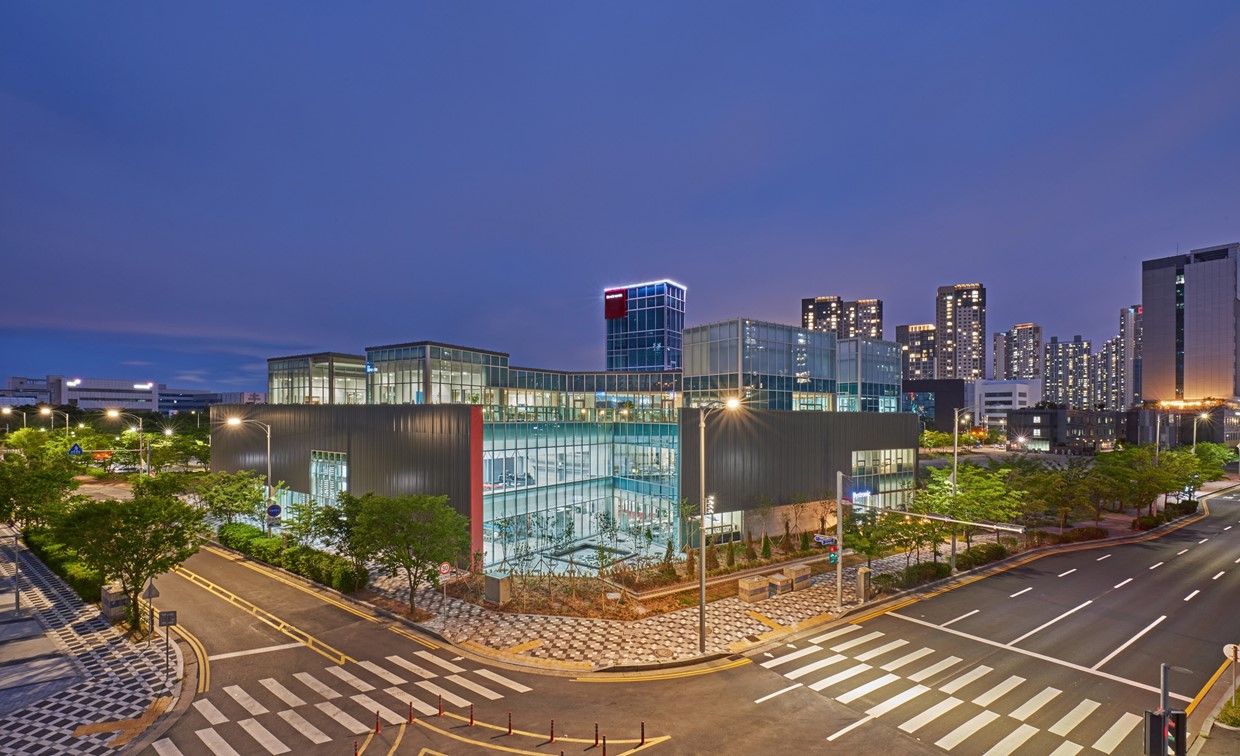
Close to our customers
Demand in South Korea has been developing positively over the last few years. Consequently, establishing a new Brand Experience Center in this region was high on our list of priorities as a means of moving closer to local customers and more effectively tapping into the market’s considerable potential.
The new site is located in a key strategic region for Bystronic: Bystronic Korea’s Brand Experience Center was built in Songdo-dong, an industrial area also known as the Incheon Free Economic Zone (IFEZ). It is situated some 50 kilometers southwest of the South Korean capital Seoul.
The economic output of the IFEZ makes up some 65% of South Korea’s GDP, and many of our customers are located in this region. The new premises are a mere 30 kilometers from Incheon International Airport, making our Brand Experience Center easily accessible to customers from other regions of Asia.
Modern building with state-of-the-art showroom
With the new building, we now have a universal service center for the APAC region. This means that our customers there now have direct access to our services. On an area of 3,360 square meters – three times what we had previously – a building with a striking glass façade has been created. It provides a new base for approximately 70 people who work for Bystronic Korea.
In the Brand Experience Center, visitors can experience the latest manufacturing systems, software applications, and services related to all aspects of metal processing. This includes live demonstrations, software and hardware training, and comprehensive consulting and support services. In addition, the site also offers the necessary space for sales and service. Our customers’ interest in the new Brand Experience Center has been strong, and feedback from the initial visitors has been overwhelmingly positive.
Innovations in the spotlight: the trade shows are back
Last year, two of our industry’s most important trade shows were finally held again in their proper format: At EuroBLECH in Hanover (Germany) and at FABTECH in Atlanta (USA) we presented our innovations to our customers.
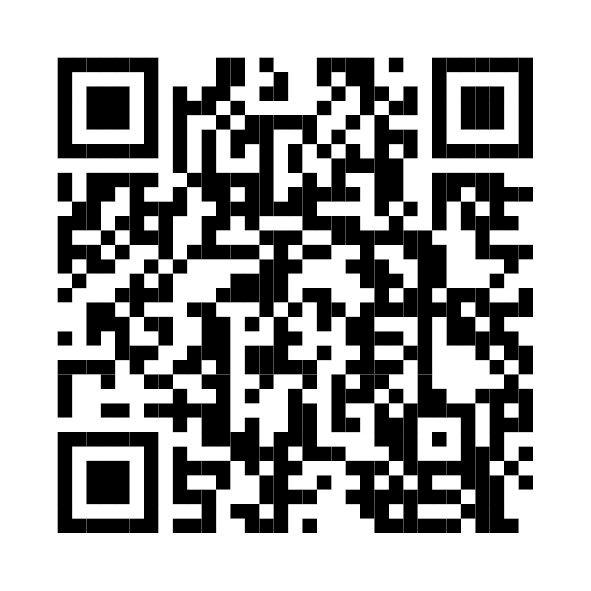
EuroBLECH 2022 in Hanover
Our participation in EuroBLECH in late October was marked by innovation and emotion. Four exhibition days, thousands of visitors and leads, excited and satisfied faces everywhere – following a four-year hiatus, EuroBLECH proved a resounding success.
Customer interest in laser cutting systems, press brakes, automation, software, services, and solutions was largely on a par with the pre-pandemic level. Bystronic staff from all around the globe were thrilled to finally be able to welcome existing and potential customers at EuroBLECH again.
More than 3,800 visitors braved a ride in our immersive “Flying Theater”. In contrast to a typical movie theater, this experience gives you the feeling of being right in the middle of all the action. Here, the audience witnessed an impressive demonstration of the way sheet metal epitomizes a material of the future, not least thanks to its potential to become a truly sustainable building block of industry. The palpable passion of so many of the visitors for sheet metal processing illustrated that our industry can look to the future with a great deal of optimism.
FABTECH 2022 in Atlanta
FABTECH in Atlanta (USA) in early November was also a resounding success. Following the 2021 edition, which was hampered by COVID restrictions, North America’s most important industry trade show was once again staged in its accustomed setting.
We showcased a wide range of products to the US audience: In the cutting segment, we exhibited the 20-kilowatt ByStar Fiber and the 12-kilowatt BySmart Fiber – both in conjunction with our ByTrans Extended loading and unloading solution – as well as the 4-kilowatt ByTube Star 130.
From our bending portfolio, we presented the ByBend Smart 160 for the very first time, showcased our flagship Xpert Pro 150, and in the field of bending automation, we featured the crowd favorite Xpert 40 in combination with a Mobile Bending Cell.
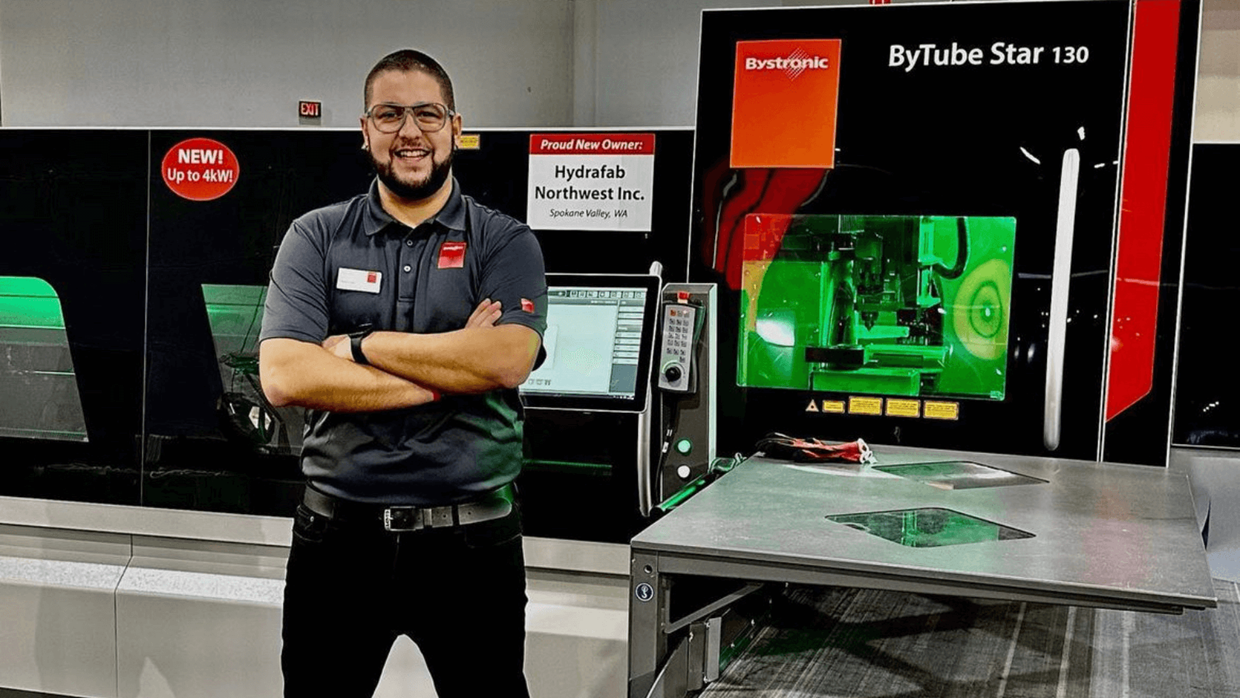
Competence Center Automation in Shanghai
The opening of our Competence Center Automation (CCA) in Shanghai (China) has enabled us to provide even faster and more effective service to our customers in China and the neighboring regions in Asia.
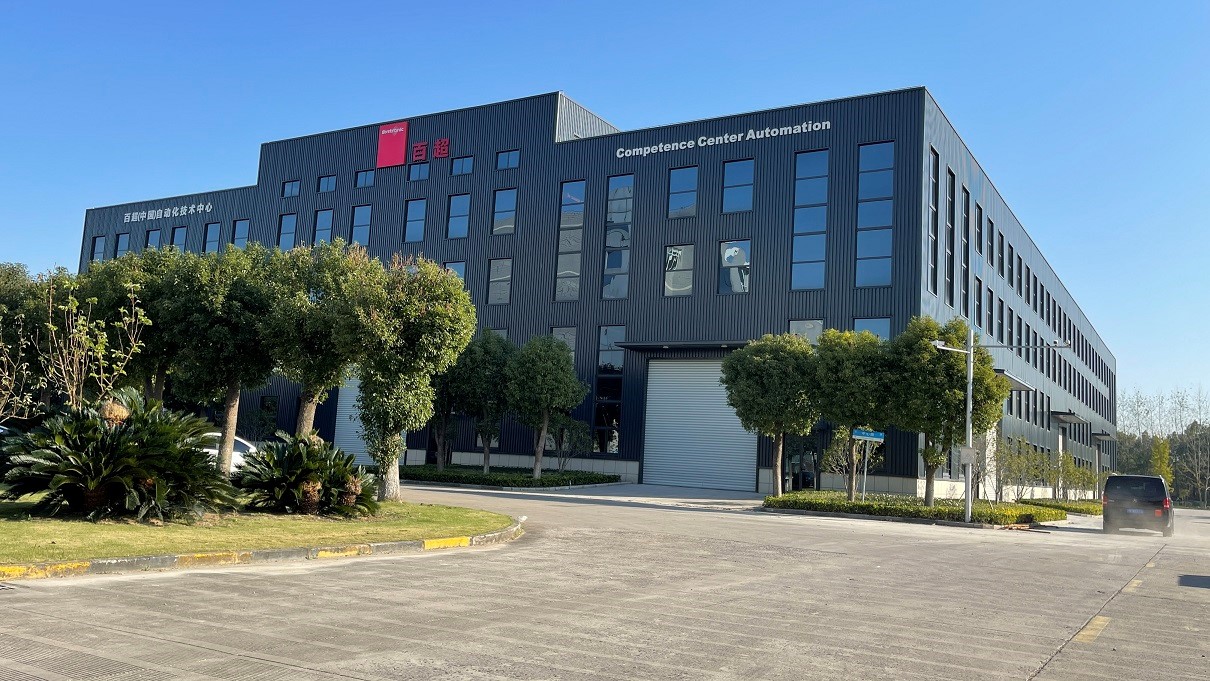
The new CCA offers automation and integration solutions for laser cutting and bending, primarily for our customers in China and other Asian countries. For customers in the Far East, this means that they can gain a more close-up impression of our automation solutions and now also have the option of purchasing more cost-effective systems.
For Bystronic, the new location speeds up the development cycle for automation products. Also, it eliminates the need for long shipping routes, and the successful integration of DNE has expanded our product range.
Expansion of the Competence Center Bending in Germany
Development and production now go hand in hand in Gotha (Germany): With the construction of the annex for the new ramp-up hall, we intend to combine the two in the best possible way.
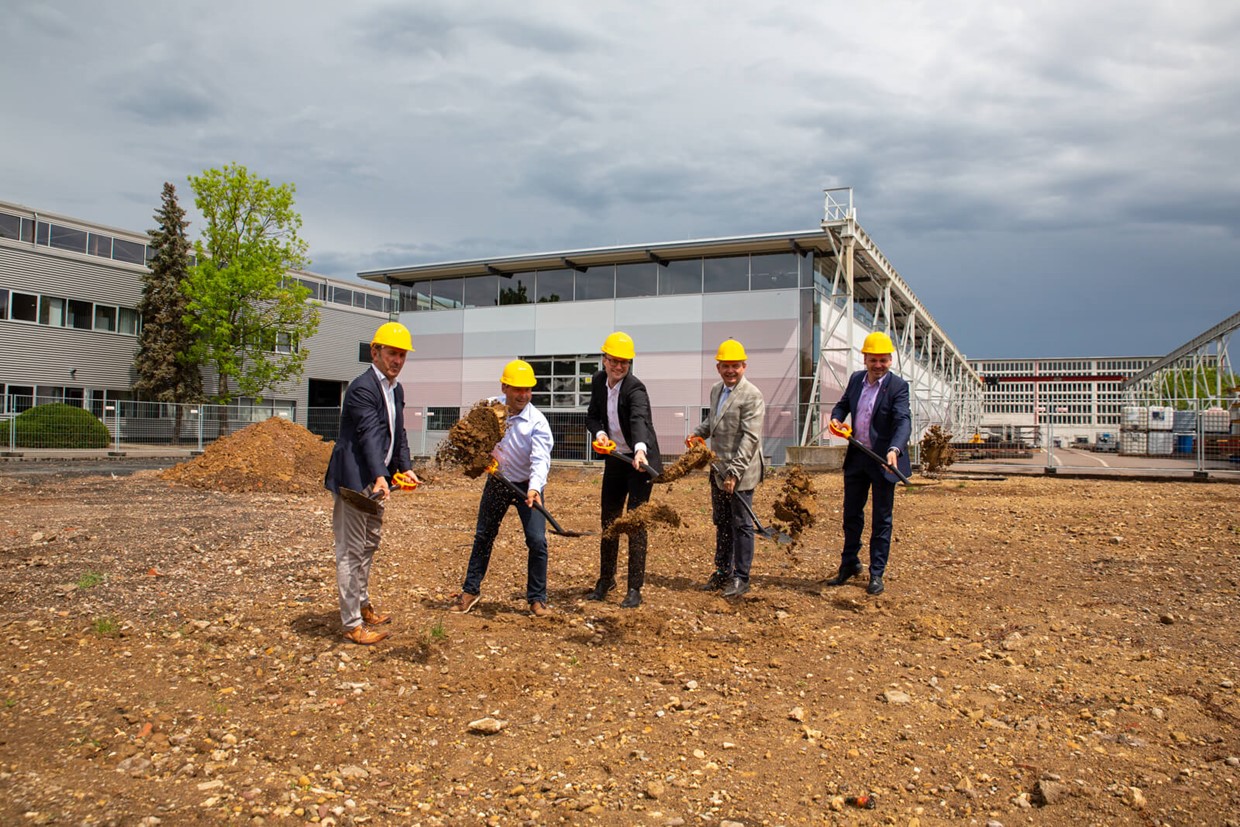
Ready to handle higher demand
In order to reduce complexity in the development and production of our bending machines, we are now using modular building blocks, which allow us to design according to customer specifications. This means we can provide our customers with optimal support and make their production more cost-effective and energy-efficient.
The growing demand for bending machines with automation solutions and modular bending cells is very encouraging. However, this also presents us with new challenges when it comes to utilizing the available space. With the new ramp-up hall, we will be able to more closely integrate development and production – from the creation of initial prototypes right through to series production.